Industry 4.0
Industry 4.0 refers to the digitalization of industrial production. On this page we deal comprehensively with the background. In addition, we explain what is changing for companies in detail.
What is Industry 4.0?
The term Industry 4.0 stands for the fourth major change in industrial history. It is a far-reaching change in industrial production, achieved through extensive digitalisation. The focus here is on the intelligent networking of processes and machines using modern communication and information technology.
Historical classification
Under the title Industry 4.0, the industry is currently undergoing its fourth fundamental change. The first industrial revolution marks the beginning of this development. It already took place in the 18th century with the use of steam engines and water power. This was followed at the beginning of the 20th century by mass production on production lines and the introduction of the assembly line. In the 1970s, the introduction of computer-assisted processes again changed the entire industry. We are currently in the fourth revolution, also known as digitalisation or digital transformation. Parallel to this, the term Industry 4.0 has become established. It was originally coined by the German federal government as part of its high-tech strategy. In the meantime, however, the buzzword has become a marketing term that is now also widely used in business and science communication.
There are some differences between the third and fourth industrial revolution. Whereas in the 1970s it was the computer that brought far-reaching changes, today it is the Internet. It is the basis for the worldwide networking of companies and the inclusion of big data in corporate decisions, and is thus the pioneer of the new industrial era.
What are the goals of Industry 4.0?
The overriding goals of Industry 4.0 are productivity increases, cost reductions and more flexible manufacturing. The latter point plays a particularly important role for the high degree of individualization of products. To achieve these goals, two developments are particularly relevant: networking and self-control. Let us take a look below at what lies behind these factors.
Networking
Networking means the system-technical connection of all people and objects involved in the production process (plants, machines, transport containers, transport equipment, intermediate products and end products). Furthermore, all partners (customers, manufacturers and suppliers) along the value chain are connected with each other. In this context, we often speak of a connection between the physical (real) and virtual world in industry. The goal of Industry 4.0 is to enable all objects and process participants to exchange data and react intelligently to each other.
Self-regulation
In the past, production facilities were centrally controlled. Information was collected in different IT systems and evaluated (interpreted) by human employees. On this basis, adjustments could then be made - for example to increase productivity or efficiency.
In Industry 4.0, this process is changing fundamentally. All machines and also the manufactured products will be equipped with communication technologies such as sensors to communicate continuously and in real-time. Objects not only exchange information with each other, but also transmit their data to various IT systems. These include production planning and control as well as maintenance, development, materials management and sales.
Smart Factory as final stage of expansion
In the final stage of Industry 4.0, the so-called Smart Factory will be created in this way. It is characterized by the fact that algorithms control all machines independently and react intelligently to current conditions. Thanks to the networking with materials management, each machine knows, for example, how many components are currently in the warehouse. If the stock is running low, the system automatically places an order with the connected supplier. Intelligent self-control in Industry 4.0 also makes it possible to react to changing customer requirements at very short notice. For example, if a car buyer decides to buy a panorama roof at the last minute, the Smart Factory independently plans a different production sequence for the vehicle.
Today's central control of industrial companies is thus giving way to intelligent (decentralized) self-optimization through algorithms. A characteristic feature here is that machines and robots not only repeat specified work steps a thousand times. Rather, they decide independently when which component takes which route through production.
Which technologies play a role in Industry 4.0?
In this section we would like to look at Industry 4.0 from a technical perspective. Specifically, the question is which technologies are necessary to realize the aspects "networking" and "self-control". In particular, the following should be mentioned:
- Communication Technologies
- Industrial Internet of Things (IIoT); especially sensor technology
- Robotics
- AI
- Additive production processes; especially 3D printing
- Big data and forward-looking analyses
- Cyber-physical systems and digital twins
- cloud computing
- ERP software, MES and APS
In the following we describe these technological aspects of Industry 4.0 in more detail due to their high relevance.
Communication Technologies
Industry 4.0 stands or falls with the transmission of data in real time (or at least in near-real time). For the most part, communication does not take place in local networks but via the Internet. In addition to stable broadband connections, a powerful mobile communications standard is required, which is currently being established in the form of 5G. However, there are other wireless transmission paths that play a role in Industry 4.0. These include:
- Low Power Wide Area Network (LPWAN)
- RFID
- NFC (Near Field Communication)
Industrial Internet of Things (IIoT)
Networking and self-control can only be realized if every object is digitally recorded and can communicate. The objects must therefore be equipped with digital storage media, communication solutions and sensors. This linking of real objects with the Internet is also called Industrial Internet of Things (IIoT) in the industrial environment.
Robotics
This technology is not new, but in the context of Industry 4.0 it gains even more importance, because without it a complete automation of production processes is hardly possible. Robots also play an important role in the individualization of production in all industries. They are becoming more and more flexible and are therefore also suitable for smaller quantities. In combination with machine learning, they are able to carry out tasks independently and to optimise themselves continuously.
Artificial Intelligence
A key technology for autonomous production processes in Industry 4.0 is artificial intelligence (AI). It is able to make deductions from patterns or recurring states. This is relevant in many areas - such as production planning, machine control and logistics (internal and external). AI also enables so-called predictive maintenance.
Additive production processes (3D printing)
An important goal of Industry 4.0 is to make production more flexible. This extends to the so-called batch size 1, the production of unique items according to customer requirements. However, this represents a challenge, especially for companies in series and mass production, because traditional production facilities are designed for large quantities. Therefore, new production processes are necessary, where the expensive conversion of plants can be avoided. 3D printing, in which the material is applied in layers, has great potential here. Individual workpieces can thus be produced without special preparation and without tools.
Big data and forward-looking analyses
Big Data refers to large amounts of data with high complexity. In Industry 4.0, this data is generated in particular by sensors. The challenge is to harmonize and correlate the data. They can then be used for analyses and forecasts. In the context of Industry 4.0, for example, the processing of Big Data enables the prediction of customer demand, the predictive maintenance of machines (see AI), and a forecast of capacity utilization in production. Last but not least, additional services or completely new business models can be realized by using existing data.
Cyber-physical systems and digital twins
Cyber-physical systems (CPS) are also a significant factor in the fourth industrial revolution. They enable a connection of the real (physical) world with virtual processes and objects. For this purpose, products, machines, plants and other objects in Industry 4.0 are given a second identity on the net - the so-called digital twin. This makes it possible to virtually network, control, test and optimize the objects.
Cloud computing
Both networking and the fast processing of large amounts of data in Industry 4.0 require extensive computing and storage capacities. These must also be scalable at short notice if required. Since this is difficult to map with in-house data centers, cloud solutions are gaining ground. These IT infrastructures are available via the Internet and are provided as services by specialized providers.
ERP software, MES and APS
It goes without saying that business management as well as logistical and production-related processes in Industry 4.0 must be managed by modern systems. From today's point of view, three types of software are particularly relevant here:
- ERP software: responsible for (automated) business processes and the connection between commercial and technical areas
- MES (Manufacturing Execution Systems): Control and monitoring of production in real time, direct connection to machine data and production data acquisition, link between ERP and production
- APS (Advanced Planning and Scheduling): advanced detailed planning and scheduling, which includes not only production but also logistics processes along the value chain
Industry 4.0: What is the current status in Germany?
Industry 4.0 is an era that has recently begun and will only reach its final form in the future. It will be several decades before the "Smart Factory" is introduced across the board.
The question of where we currently stand is answered, for example, by the "German Industry 4.0 Index", which is published by Staufen AG. According to this index, in 2018 43 percent of all companies had experience with digital transformation through operational projects. 9 percent are already implementing Industry 4.0 comprehensively. Only 24 percent still belong to the group of "observers".
According to the study, predictive analytics is discussed most frequently - followed by smart data and artificial intelligence. According to the survey, 16 percent of the companies are already able to implement lot size 1 at the cost of series production.
The industry association Bitkom published the following figures in April 2018, which also provide information on the status of industry 4.0 in Germany:
- 24 percent of all machines are connected to the Internet
- 49 percent of companies use industry 4.0 applications
- The top 3 motivating factors are improved processes, improved capacity utilisation and lower production costs
- 72 percent fear high costs for data protection
Examples from the economy for industry 4.0
Examples from the economy show what is already possible in Industry 4.0 today. For example, the fan and motor manufacturer in Baden-Württemberg uses ebm-papst SAP Manufacturing Execution (SAP ME) to digitize production and network with customers and suppliers. The data exchange between the production machines and SAP ME is autonomous. Among other things, this enables the performance of production to be monitored in real time. In addition, all components can be traced from the supplier to the customer.
The technology company HARTING is a pioneer in terms of Smart Factory. It has implemented the flexible production of a connector. Customers can individually configure and order this component via a shop system. Among other things, customers have the option of assigning the connector their own identification (e.g. material number). The order is processed in an SAP system. The subsequent production process, which is also planned and controlled by SAP software, is fully automated.
What are the advantages and disadvantages of Industry 4.0?
Overall, Industry 4.0 is accompanied by far-reaching changes for companies, customers and employees. Besides enormous opportunities, there are also risks.
Opportunities and risks of Industry 4.0 from a human perspective
Every industrial revolution has led to the loss of jobs, but new professions have also been created. This is also true of the fourth industrial revolution. Here it can be assumed that jobs will be lost in production and logistics. In the medium term, routine activities that can be performed particularly well by intelligent machines will be particularly affected. For the remaining employees, however, the extensive technical support in the Industry 4.0 environment also has advantages. They are relieved of physically heavy and monotonous work and gain freedom for higher-value activities. Shift work becomes unnecessary and working hours can be arranged more flexibly. We are also talking about Work 4.0 in this context.
Opportunities and risks of the industry 4.0 from the perspective of the companies
Industry 4.0 offers considerable potential for companies. On the one hand, resources (including employees) can be saved, and on the other hand, productivity and efficiency in manufacturing can be increased considerably. In addition, the digital change will make it possible to produce very small series and even single pieces without high additional costs. This is an important factor in terms of customer satisfaction. Last but not least, data can be used to develop new services or business models. The possibilities offered by Industry 4.0 here extend to the development of completely new market segments.
However, these opportunities also face challenges that we would like to look at in more detail below.
What challenges does Industry 4.0 bring to medium-sized companies?
Challenges arise from Industry 4.0 basically for companies of all sectors and sizes. However, the digital transformation is particularly difficult for medium-sized companies. Here the budgets for automation technologies, new systems and high-performance networks are naturally rather limited. In addition, the profitability of such investments is difficult to estimate in advance. On the other hand, too much hesitation can mean a loss of competitiveness sooner or later.
A further challenge of Industry 4.0 is the change in the world of work. Employees whose previous tasks are no longer necessary due to automation must be retrained to offer them new perspectives. In general, the change requires good change management in order to pick up the people affected, to reduce fears and to introduce them to new forms of work.
Another risk of Industry 4.0 that should not be underestimated is in the areas of data protection and data security. Medium-sized companies in particular, which were previously hardly networked at all, have to overcome major hurdles in this area. On the one hand, high investments in IT security are required, while on the other hand know-how must be built up. However, there is already a blatant lack of IT specialists, which is why there is usually no way around cooperation with external IT security specialists.
What solutions does SAP offer for Industry 4.0?
Manufacturing companies are traditionally among SAP's customers. It is therefore only logical that the leading Walldorf-based software group has an extensive portfolio of solutions for Industry 4.0. The components of the "SAP Digital Manufacturing Suite" are particularly noteworthy:
- SAP Digital Manufacturing Cloud
- SAP Manufacturing Execution
- SAP Manufacturing Integration and Intelligence
- SAP S/4HANA Manufacturing
How these solutions are used in the context of Industry 4.0 is described in the following sections.
SAP Digital Manufacturing Cloud
SAP Digital Manufacturing Cloud is a cloud-based manufacturing execution system that enables the consolidation of data from SAP ERP systems and manufacturing systems as defined by Industry 4.0. The software thus combines business and manufacturing processes. It also enables you to monitor and analyze manufacturing data (IoT) in near real-time. This significantly increases transparency with regard to current manufacturing performance.
SAP Manufacturing Execution
SAP Manufacturing Execution is also a production control system that works seamlessly with SAP ERP. It enables central monitoring and control of production and assembly. In addition, it offers possibilities for automated data collection from the Internet of Things, a basic requirement for Industry 4.0.
SAP Manufacturing Integration and Intelligence
SAP Manufacturing Integration and Intelligence is a web-based platform for so-called vertical integration. This term refers to the integration of different IT systems (e.g. IoT sensors, production control/shop-floor systems, business planning) in a continuous solution. This SAP software thus creates an important prerequisite for the Smart Factory in Industry 4.0: the networking of all data sources and processing systems in the company. SAP Manufacturing Integration and Intelligence also maps important KPIs for production control. These relate in particular to the factors efficiency, availability and quality.
Industry 4.0 with SAP S/4HANA Manufacturing
SAP S/4HANA Manufacturing is a solution for the fully integrated handling of manufacturing processes and thus the implementation of Industry 4.0, including production planning as well as the consolidation and control of the actual production. It also includes functions for quality management and maintenance. Furthermore, the connection of external partners such as suppliers and subcontractors is possible (horizontal integration). In SAP S/4HANA Manufacturing, all the tools are available to realize fully automated production and lot size 1.
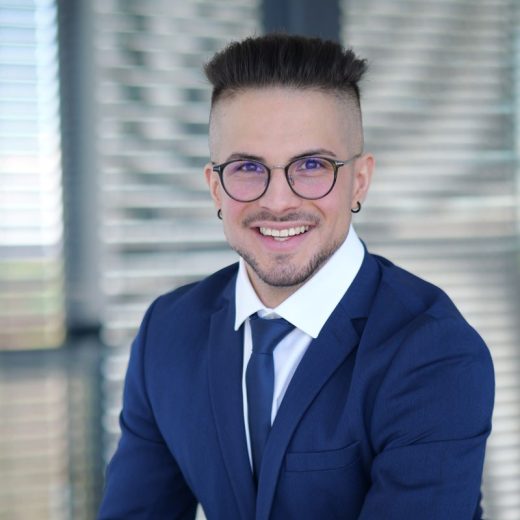
Emre Cetin, Sales Executive
Do you have questions about SAP? I am happy to help!+41 41 784 19 31